Sustainable rubber harvesting, manufacturing, and repurposing is an ever-present challenge within the rubber industry
As such, industry leaders like AirBoss constantly reassess processes to improve efficiency and reduce waste.
For AirBoss’s Erin Stavropoulos, Director of Sustainability, this kind of organizational responsibility is spurred by internal initiatives as well as customer expectations. She explains that optimizing manufacturing practices while finding ways to repurpose rubber has always been a priority for the company.
“A small adjustment to the formulation of a compound can often improve the performance characteristics of a compound or solve a quality issue which has presented itself,” says Stavropoulos. “We always want to do that when we’re able to. Improving compounds in this way also obviously helps to reduce our waste.”
Rubber – like many materials used in modern manufacturing – has had a long history peppered with efforts focused on sustainability. Both manufacturers and consumers continue to try and reduce the impact which manufacturing has on the environment, and companies like AirBoss help advance how the industry recycles and repurposes rubber.
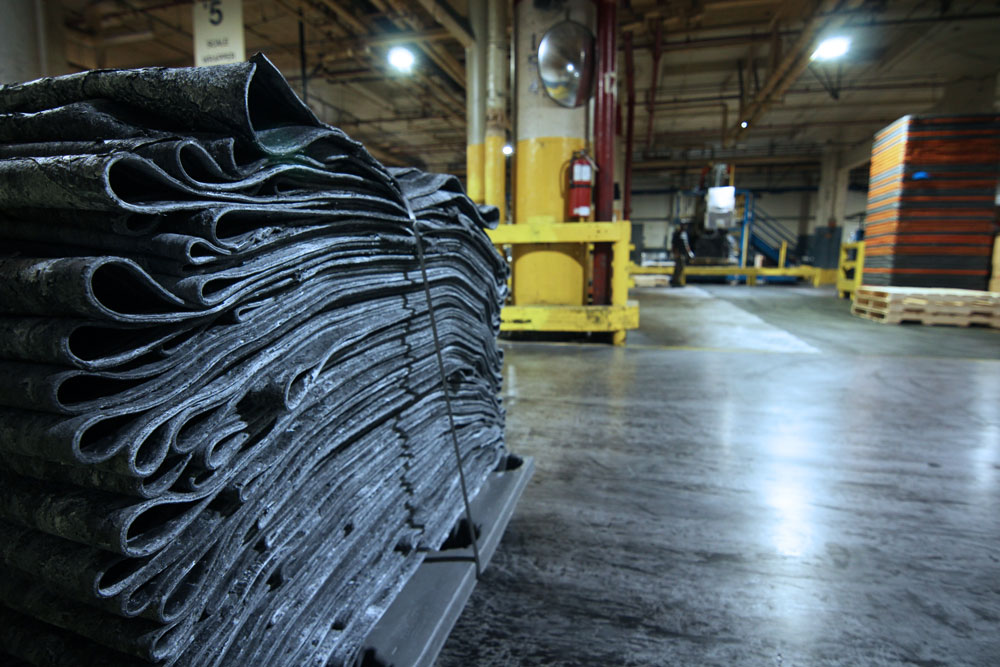
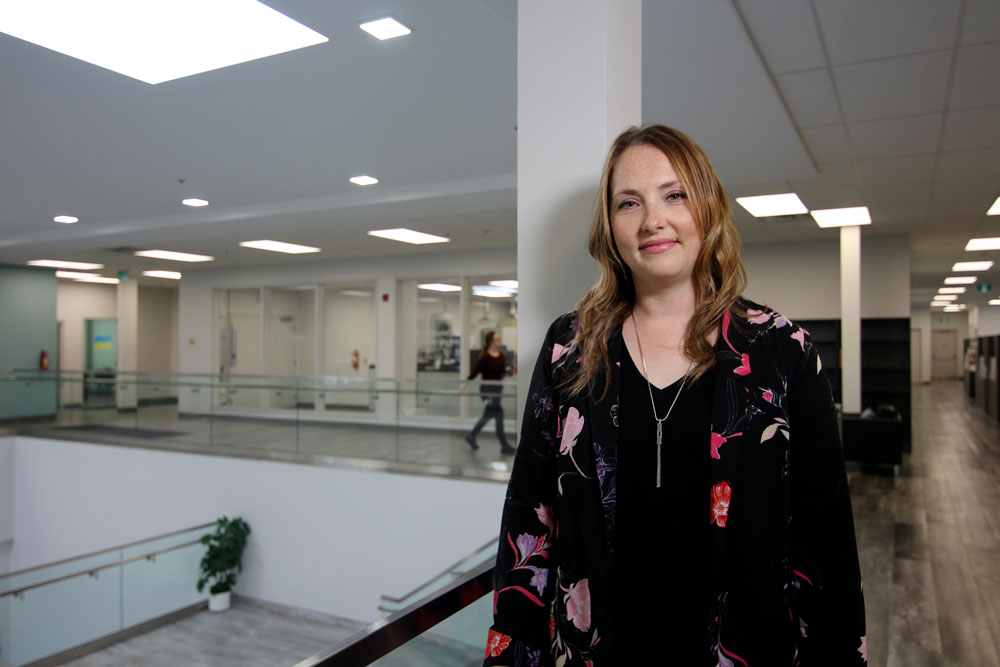
Traditional Rubber Repurposing
Repurposing is a practice that’s been around almost as long as rubber production.
Early iterations of the raincoat, developed by Charles Macintosh in the early 1800s, used a rubber solution to make wool waterproof, and Macintosh needed a lot of rubber. This, in turn, led to the development of a machine called the masticator.
This machine essentially chewed up large pieces of rubber into smaller bits. These bits could then be reprocessed. Unfortunately, if not ironically, with the advancement of technology came the end of “easy” reprocessing.
Vulcanization – a process that made rubber stronger and more durable – made recycling the material harder and more complex. Additionally, the price of rubber dropping during the mid-to-late-1900s meant investing in recycling was less profitable.
Unfortunately, this meant lots of rubber went to landfills (it’s probably not hard to imagine the trash tire piles of the mid-1900s), and the responsibility of repurposing was left mainly to manufacturers.
Modern Rubber Recycling
The ideal manufacturing, molding, and rubber compounding scenario would include zero waste and complete sustainability. It’s a lofty goal and one that modern manufacturers like AirBoss continue to work towards.
As a result, the reduction of waste and the repurposing, recycling, and reusing of rubber mixtures are all par for the course at this point.
Remixing Non-Conforming Compounds
Often, the first step in a rubber manufacturer’s recycling process is to determine if a mixed compound can be remixed. This is usually dependent on customer specifications and the manufacturer’s capabilities.
“We can take a whole batch of material and we can put that back into the mixer with some adjustments to the chemicals and mix it again,” explains Stavropoulos. “That way, we can entirely repurpose the original batch.”
Remixing non-conforming compounds is a process that’s made easy when enterprise-level rubber manufacturers like AirBoss can alter a few parameters, mix in different additives, and create a new compound. It’s about as close to zero waste as you can get.
Selling, Recycling, and Repurposing Rubber
Selling excess rubber and/or a non-conforming compound to companies that can recycle it into different products is another way some manufacturers repurpose their material. Some of these third-party processors make flip-flops with it while others make things like rubber flooring. Typically, these companies recycle rubber into lower-grade products.
Lower-grade doesn’t necessarily mean cheap.
Not all manufacturers have the capability, technology, or expertise to reprocess rubber. These companies instead create less complex products that don’t have to adhere to the same restrictions, regulations, or quality requirements that AirBoss or our proprietary customers do.
“It’s another way of keeping it out of landfills,” Stavropoulos says of this kind of rubber repurposing.
Contact Our Global Experts
Learn more about how we can make a material difference in your business, contact our world class staff for more detailed information.
AirBoss is Committed to Monitoring and Improving Sustainability
Stavropoulos and AirBoss have long been committed to improving sustainability, recycling, and efficiency efforts within the company. As a result, AirBoss works with partners who have similar sustainability goals when it comes to repurposing rubber and/or remixing non-conforming compounds.
Fortunately, Stavropoulos is the tip of the spear, so to speak, when it comes to leading those efforts as Director of Sustainability. It’s not a responsibility she takes lightly.
“I’m working on our annual sustainability report, which we expect is going to encompass all of the data for ESG across all of our divisions this year,” she explains. “We’re expanding the scope to include energy and emissions data. Last year we did this for our Kitchener facility, and this year we’re including everybody and trying to get a more robust picture of our sustainability.”
The 2021 sustainability report for the Kitchener facility was released in March 2022 and, according to Stavropoulos, has paved the way for annual improvements. Although it’s not a new idea at AirBoss to define sustainability goals, it’s one that has seen a renewed dedication in recent years.
“Customers have been impressed with what AirBoss does in terms of sustainability,” says Erin Stavropoulos. “We’re focusing on this now more than ever, and there’s been good feedback.”
Modern technology coupled with improved manufacturing processes – like automatic weighing of mixture chemicals and more efficient machinery – means that it’s easier for AirBoss to reduce waste, optimize process control, and improve rubber recycling.